A Dynamic Production Environment Requires Innovative Dosing Technology
Dosing experts have long known: To achieve efficient dosing, rheological influences must be minimized as much as possible. With this goal in mind, the four-person team at ViscoTec tackled a project for an Austrian food company. The company produces fitness bars that are enhanced with a topping on the upper surface. For this specialized processing step, the company brought in ViscoTec to design, build, and commission a five-lane dosing system within approximately 18 months.
Precision and Efficiency: A Challenge at 100,000 mPas
With a viscosity exceeding 100,000 mPas, conventional piston pumps are not suitable for dosing these highly viscous toppings. They tend to create stringing effects, leading to material waste and quality issues – none of which are desired for this premium snack manufacturer.
Another challenge for ViscoTec’s engineers: Each batch contains bars of varying lengths. The dosing process must function seamlessly despite this variability while maintaining a consistent production speed to ensure continuous conveyor belt operation.
Advanced Control Technology Enables an Efficient Solution
The topping is applied using a system based on the endless piston principle. This allows for pulsation-free and gentle application in the automated bar production process. High repeatability and ultra-precise dosing with minimal dead space ensure consistently verifiable product quality.
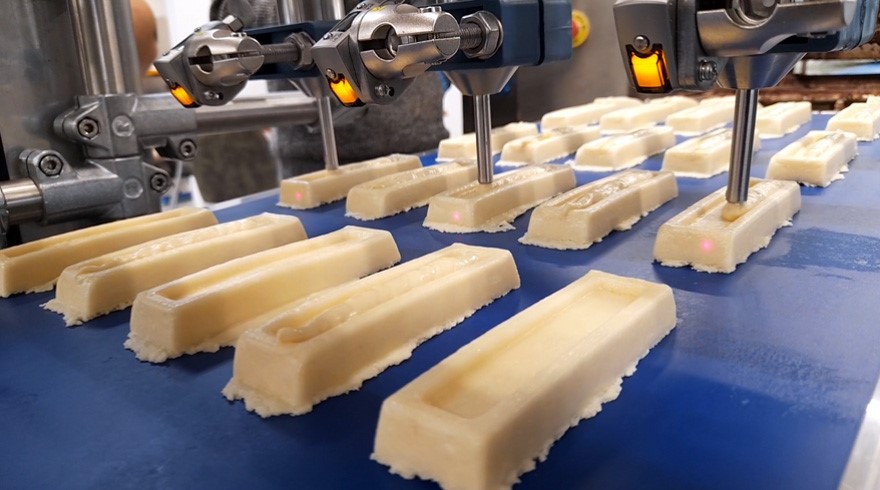
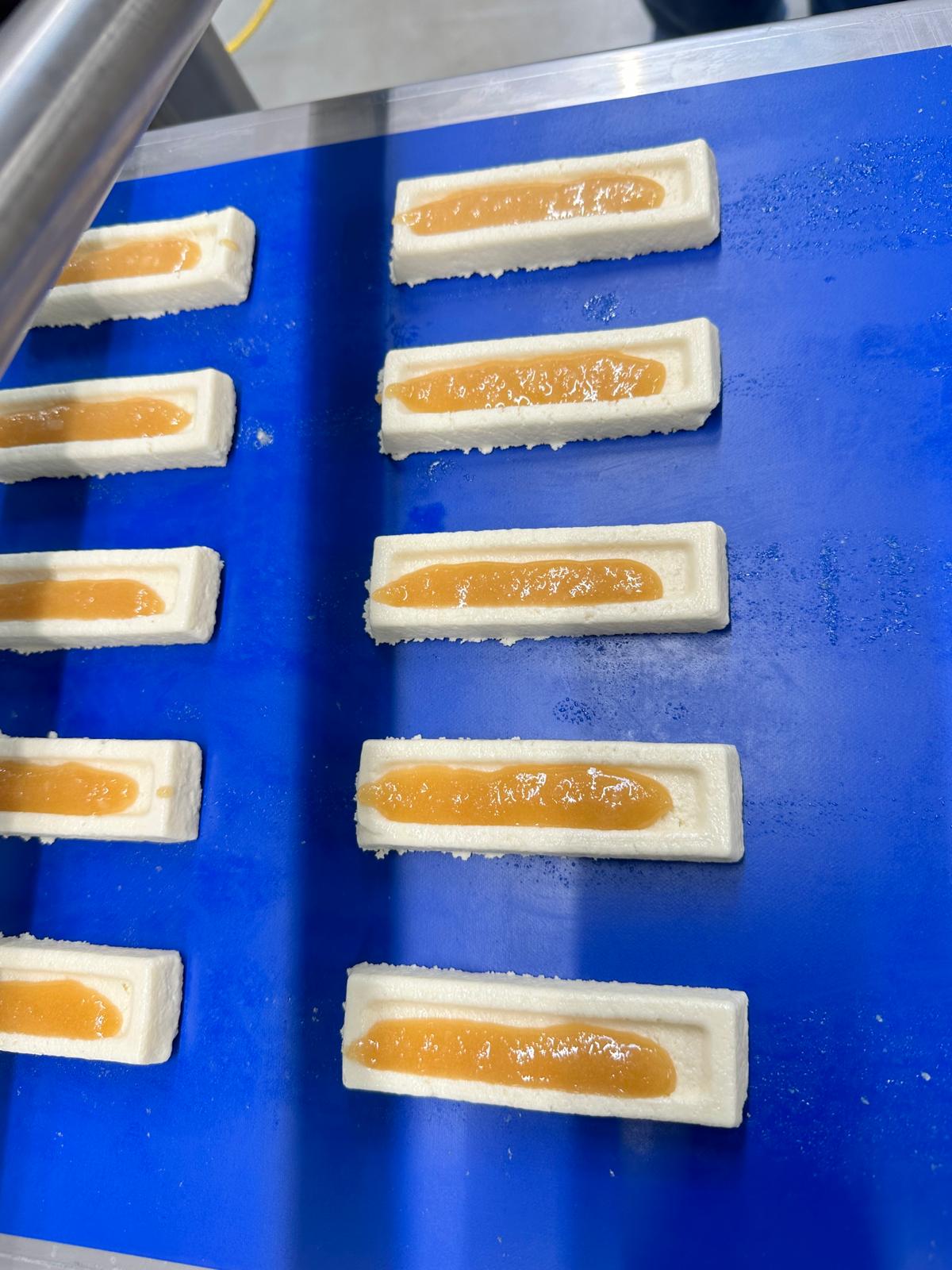
In collaboration with the system integrator, the ViscoTec team developed a production line with the following process: Dough bars are transported directly from the mixer to the dosing system via a conveyor belt. An optical sensor detects each individual bar and triggers the dosing process. Valveless dispensers ensure the reliable application of the highly viscous topping. As soon as a bar is positioned under a filling nozzle, the dosing pump starts. The topping is applied. Each pump operates independently, activating as soon as the sensor detects a bar beneath the nozzle.
A key advantage of the endless piston principle is the ability to adjust the dosing quantity in real-time: As long as the sensor detects a bar, the pump continues dosing, allowing for the precise application of topping even on bars of varying lengths within a batch. Once the bar leaves the detection area, the pump stops. An adjustable retraction mechanism prevents stringing, eliminates topping waste, and ensures a uniform bead shape — even with differently sized bars — a must for premium products.
Customer Benefits: Performance and Reliability
Unlike conventional systems, the ViscoTec dosing system does not require a synchronized stop-and-go operation of the conveyor belt. This significantly increases production efficiency and enables smooth, high-speed filling. By combining precise control, flexible dosing volume adjustment, and reliable handling of challenging materials, the company has found a powerful and dependable solution tailored to its specific requirements.