With ViscoTec’s vipro-CONTROL, customers benefit from a control system based on Siemens Simatic-S7 components, ensuring flexibility through a variety of additional functionalities. One prominent application of this system is in the battery production processes of Webasto, a top-100 automotive supplier.
Key vipro-CONTROL Features for the Supplier
One of the primary advantages of vipro-CONTROL lies in its enhanced precision functions, notably the “Override” feature. This functionality, utilized by Webasto in their robotic bead application, scales the dispensing speed according to the robot’s movement speed. The result: uniform and consistent material application, even around curves. High-precision servo motors with integrated encoders ensure accurate rotor position detection.
Standard vipro-CONTROL features include tracking specific dispensing counts, dispensing times, and cumulative dispensed volumes. Alarm thresholds for calibration, maintenance, and dispensing counters can be parameterized. In 2K systems, an additional counter for purge shots is also available.
The process flow can be tested without material using a drive simulation, where the dispensing control simulates expected feedback from a drive. Various user levels help prevent operational errors.
Advanced purge functions were especially critical for Webasto, focusing on pot life monitoring and single-component purging. High-quality dispensing demands adherence to material-specific pot lives, during which mixed components must react and be processed. For 2K materials, downtime due to hardened material in the mixer must be avoided. This is managed by enabling integrated pot life monitoring, which automatically triggers a purge shot before the pot life expires. Manual interventions and warning confirmations are handled via the HMI.
Single-component purging, available on the technical user level, prevents material from being pushed from one mixer chamber to another. A material-saving feature is the segmented purge shot, which only flushes the mixer segment where the pot-life-dependent purge interval has expired. The result: minimal waste of dispensing medium, reducing scrap over time.
Comprehensive Reporting for Customers
Webasto implements detailed reporting of all parameters via data logging, enabled by vipro-CONTROL. Every dispensing operation is logged with all relevant details (dispenser types, recipe parameters, actual dispensing values, and pressure values). The DataLog, a CSV file, is accessible via the PLC’s web server for diagnostic purposes.
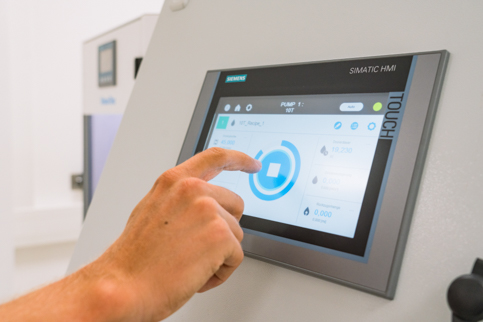
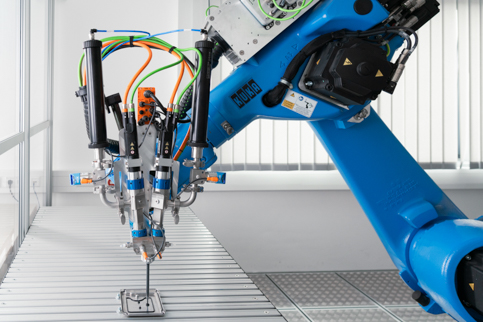
Additional Benefits for Complex Dispensing Applications
With vipro-CONTROL, users can configure up to 100 different recipes per dispenser. Recipes can be copied within or across dispensers in multi-dispensing setups. External interfaces allow recipe selection and modification of dispensing parameters, while recipe parameter limits are calculated based on pump type and calibration.
Three consecutive calibration shots within a tolerance range simplify the determination of calibration factors. For 2K dispensing, each component is calibrated separately. Recipes remain editable after calibration, and a warning is issued if an uncalibrated recipe is loaded—dispensing remains possible.
vipro-CONTROL also offers extensive safety features. Users can set four switch points for warnings and emergency shutdowns via analog sensors directly on the HMI, eliminating the need for sensor adjustments. Different user levels ensure parameter adjustability and secure operation. A dry-run protection system evaluates input pressure to prevent material shortages, safeguarding the system. Additionally, an overpressure sensor at the pump outlet prevents clogs and critical conditions. Visualization is provided directly in the device overview.
Seamless Line Integration Through Optimized Interfaces
The vipro-CONTROL communicates with higher-level process control systems, allowing external calibration. This is particularly advantageous in multi-unit systems with centralized control. The dispensing control features a dedicated operating mode for this purpose. Parameters such as dispensing mode (volume or start-stop), dispensing volume, and speed can be adjusted via external interfaces, with checks performed in a dedicated section. The interface also loads and assigns recipes to specific dispensers. Various data points—such as current recipe parameters, commands, and dispensing data like pressure sensor values—are transmitted to the higher-level control system.